Recalls. A term that can strike fear into even the most tenured product and brand managers.
It conjures up images of dramatic headlines, cratering share prices, ruined consumer confidence and legal action with enormous payouts.
In reality, this is a fairly extreme scenario. The vast majority of recalls (80-90% of drug recalls, for example) are considerably less severe. Many product recalls will go completely under the radar for all but your most engaged customers.
To differentiate between recalls of products that pose a risk to life and health and those that only hold minor defects or labeling issues, they are split into different tiers – or classes – by government agencies.
In this article, we discuss these different tiers, with examples given for each, so you can visualize what a product recall might look like for your business.
The different classification systems
Depending on which government agency oversees your products, recalls will be split into either three classes or just two.
Three tiers
To generalize, three-tier systems are issued by agencies that oversee everyday products, such as food and consumer goods (but not vehicles). These include:
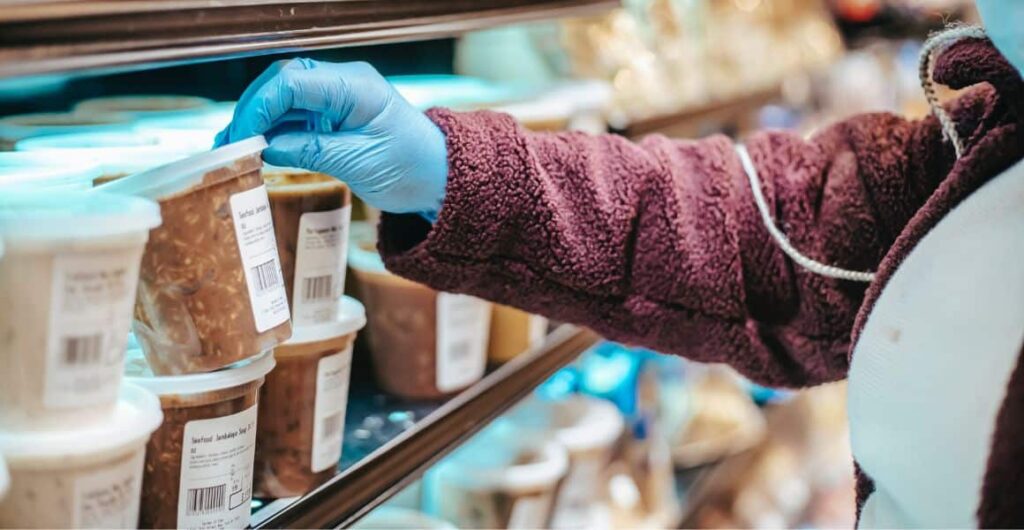
Two tiers
The two agencies that separate their recalls into two tiers are both concerned with transportation safety, specifically road vehicles and aircraft.
For the purposes of this article, we will only be discussing the three-tier classification systems.
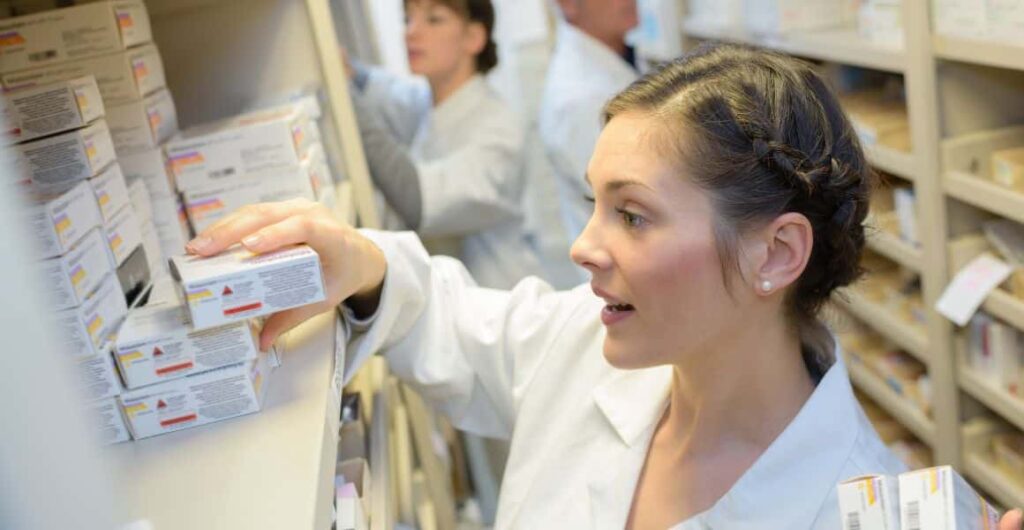
Classifications
Class I/High hazard
Class I/High Hazard recalls are the most serious forms of product recall in the U.S. They are issued in “a situation in which there is a reasonable probability that the use of, or exposure to, a violative product will cause serious adverse health consequences or death.”
In short, a Class I recall will be issued if a product could cause serious injuries, life-threatening conditions, permanent impairment or death. These recalls typically involve returning or disposing of the defective product and the manufacturer issuing a refund or replacement.
Frequency of Class I/High hazard recalls
Only between 5-15% of all recalls receive a Class I classification. Despite that statistic, if you asked most people to explain a “product recall,” this would be what they describe. That is largely because high hazard recalls receive a lot of attention in the media, due to the severity of the associated risks.
Examples
Philips ventilators
In 2021, Philips Respironics recalled millions of Continuous Positive Airway Pressure (CPAP) and Bilevel Positive Airway Pressure (BiPAP) ventilators due to concerns about the soundproofing foam used. The foam could degrade over time, with particles breaking off and toxic chemicals being released that could be inhaled by users, causing respiratory irritation and an increased risk of cancer.
18 models manufactured between 2007 and 2022 were initially involved in the recall. In 2022, additional BiPAP ventilator models were added because of concerns about plastic motor components releasing harmful chemicals. It’s unknown exactly how many individual units have been recalled, but in September 2023, Philips settled a class action lawsuit, agreeing to pay a minimum of $479 million to those affected.
Fisher-Price Rock ‘n Play Sleeper
In April 2019, 4.7 million sleepers were voluntarily recalled by Fisher-Price, working with the CPSC. The sleepers’ design meant that babies could roll onto their stomach while unrestrained, increasing the risk of suffocation. Years of warnings from pediatricians, parents and foreign regulators had been ignored before this recall was initiated. The Rock ‘n Play Sleeper is now estimated to have been responsible for around 100 infant deaths since its release in 2009.
It was later discovered that Fisher-Price only consulted a single physician before bringing the Rock ‘n Play to market. Adding insult to injury, that doctor wasn’t even a pediatrician and was later accused by the Texas Medical Board of practicing medicine without a license.
2009 peanut butter recall
In the most extensive food recall in U.S. history, over 3,900 different products manufactured by 361 different companies were recalled due to contamination with salmonella. Nine Americans had been killed by the contamination and at least 714 had been sickened. Everything produced at Peanut Corporation of America’s (PCA) plant in Blakely, Georgia, since 2007 was recalled. This included some school lunches and even emergency meals distributed by FEMA after a massive ice storm.
Less than 24 hours after the recall announcement, PCA filed for Chapter 7 bankruptcy. Following an FBI investigation, PCA’s president, Stewart Parnell, and his brother Michael were found guilty of fraud, conspiracy and other charges. Stewart was sentenced to 28 years in prison and Michael 20 years.
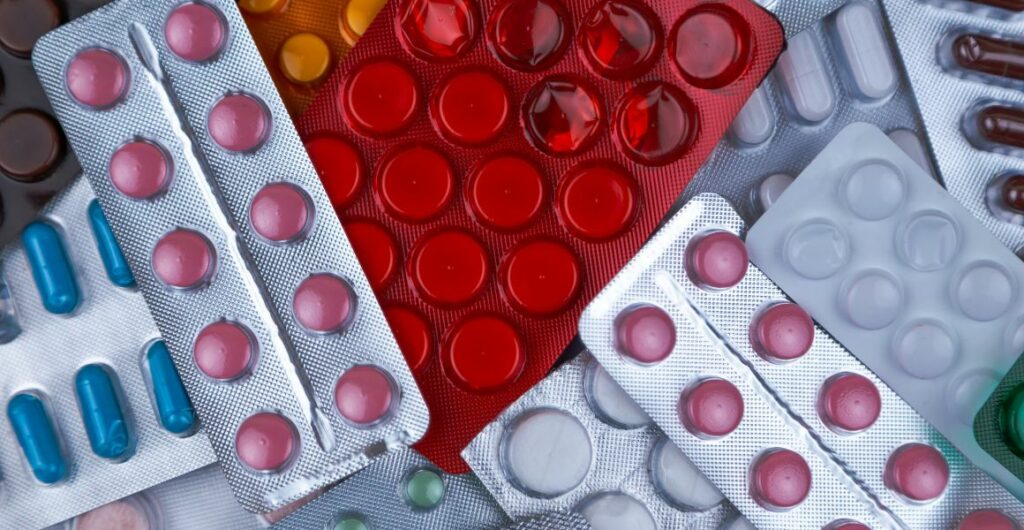
Class II/Moderate hazard
A Class II recall signifies a situation where using or being exposed to the product may cause temporary or medically reversible health problems. The probability of serious adverse health consequences is remote.
Consumers may be advised to stop using the product, or may be allowed to continue using it with caution.
Frequency of Class II/Moderate hazard recalls
Class II recalls are the most common type of recall, comprising between 40% and 70% of all recalls, depending on industry.
Examples
IKEA MALM dressers
IKEA recalled taller models of their MALM chests and dressers in 2016, following four child fatalities. If not anchored to a wall, the dressers were found to be prone to tipping over when climbed on by children. This recall was only Class II, as fatalities would not occur when the dresser was used correctly, and the danger could be easily mitigated through warnings or simple anchoring kits.
IKEA faced lawsuits from families whose children had been crushed by MALM furniture, but there was no push for consumers to stop using the products. IKEA offered refunds and free wall-anchoring kits. The MALM line has since been discontinued.
Beyond Meat Burger metal object contamination
Beyond Meat recalled specific lots of their Beyond Burger plant-based patties in September 2020, due to the potential presence of metal objects. Consumers had reported finding metal objects, like fragments of metal mesh or gear teeth, embedded in the Beyond Burger patties.
The recall was eventually deemed successful, with a significant portion of the affected products retrieved and no reported injuries resulting from the contamination. The exact cause remained unclear, with possibilities ranging from equipment malfunction to supplier issues further up the distribution chain.
Allergan Biocell textured breast implants and tissue expanders
Millions of women worldwide had received Biocell implants before the recall was requested from Allergan by the USDA in July 2019. The implants had been linked to breast implant-associated anaplastic large cell lymphoma (BIA-ALCL), a rare cancer.
Despite the risk of such a serious health condition, this was only a Class II, not a Class I recall, as the overall risk was considered low.
Class III/Low hazard
Class III/Low hazard recalls are issued for products that are “unlikely to cause injury or illness, but not conforming to regulations.” Class III recalls are the least severe form of recall.
Frequency of Class III/Low hazard recalls
They are also the least common variety of recall, and because they are rarely mentioned in the media, they often have very little impact on consumer trust and brand reputation. Class III recalls are also by far the least expensive to remedy.
Examples
Class III recalls are initiated by the manufacturer rather than an overseeing government agency. This is because they involve products that aren’t likely to cause adverse health consequences, so the potential harm associated is minimal and there is no reason for an agency to demand a recall.
As a result, there are very few newsworthy examples, simply because there is little public interest and the news of the recall rarely spreads. For example, if a company sold a product that turned out to be faulty, but did not pose a risk to human life or public health, they might still issue a recall to prevent damage to consumer trust and brand reputation.
Likewise, if an error was found in the insert that came with a box of painkillers, but that error didn’t risk consumers using the painkillers incorrectly and damaging their health, the manufacturer might still issue a recall.
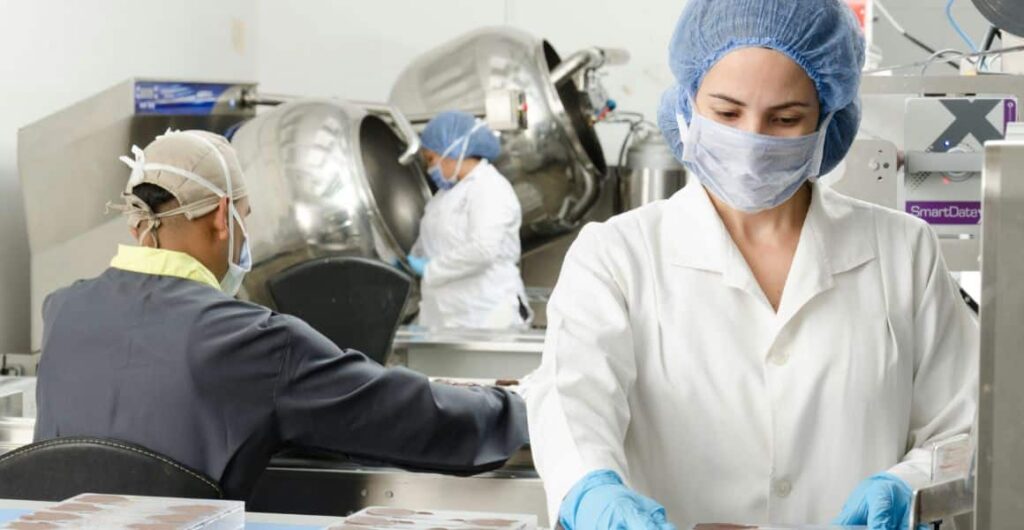
Voluntary recalls
Not all recalls are demanded by a government agency. Sometimes manufacturers will begin the recall process themselves in order to save face and prevent damage to their brand’s reputation. This is known as a “voluntary” recall, as opposed to a mandatory recall.
Whether a recall is voluntary or mandatory isn’t directly linked to its classification, other than the fact that no Class III recall will be mandatory. Many Class I recalls are voluntary (at least at first). However, a voluntary recall can become mandatory if it is deemed to be ineffective, the risk of harm to the public escalates or there is significant public pressure.
Final thoughts
While “recall” may still have strong negative connotations in the minds of the general public, a proactive recall that is well-executed can minimize the damage and even earn some trust and confidence from your consumers.
On the other hand, sticking your head in the sand or denying that a recall is needed for too long can be devastating and opens your brand up to accusations of prioritizing revenue over the safety and wellbeing of your customers, as can a poorly executed recall.
Ensuring that a recall is handled effectively is essential, whether it’s voluntary or mandatory. At Harte Hanks, we provide a holistic recall service. We don’t just handle the fulfillment of coupons or the retrieval of defective product. Our in-house customer care department can take the strain off your helplines during this difficult time, while also monitoring consumer sentiment so you can make informed decisions about your next steps.